Understanding Bending in Sheet Metal
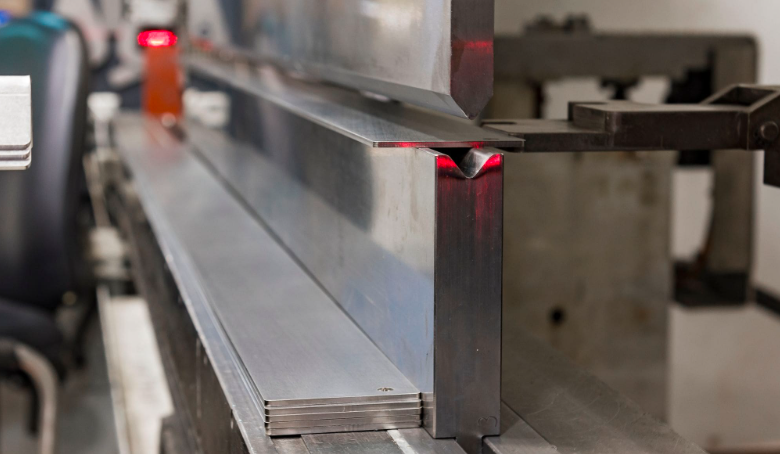
Bending in Sheet Metal is a crucial fabrication process used to shape metal sheets into desired forms without cutting or removing material. This technique is widely employed in industries such as automotive, aerospace, construction, and electronics to create components with precise angles and curves. By applying force through various bending methods, manufacturers can achieve durable and functional designs that meet specific engineering requirements.
In this article, we will explore the bending process in sheet metal, the different bending methods, key factors affecting bending quality, applications, advantages, challenges, and modern advancements in bending technology.
What is Bending in Sheet Metal?
Bending in sheet metal refers to the process of deforming a flat metal sheet along a straight axis to achieve a specific angle or shape. This is done without altering the material’s thickness or cutting it, making it a cost-effective and efficient way to produce complex structures. The bending process relies on external force applied by tools such as press brakes, dies, or rollers to create bends while maintaining the sheet’s strength.
Depending on the required shape, bending can be used to produce U-shaped, V-shaped, or curved profiles. The process is commonly performed at room temperature, making it a cold-working method that retains the material’s mechanical properties.
Key Factors Affecting Bending in Sheet Metal
Several factors influence the success and precision of bending in sheet metal. Understanding these aspects helps manufacturers achieve consistent and high-quality results.
1. Material Properties
Different metals have varying bending characteristics. Aluminum, steel, copper, and stainless steel respond differently to bending forces due to their ductility and hardness. Softer metals like aluminum are easier to bend, while harder materials require higher force.
2. Sheet Thickness
Thicker sheets require more force and specialized equipment to bend without cracking. The bending process must be carefully controlled to prevent material failure.
3. Bend Radius
The inner curve of the bend is known as the bend radius. A smaller bend radius increases the risk of material cracking, while a larger radius ensures smoother bending. The bend radius should ideally be at least equal to the sheet thickness to avoid defects.
4. Springback Effect
After bending, the sheet metal may slightly return to its original shape due to its elastic properties. This is called springback, and manufacturers compensate for it by slightly overbending the sheet.
5. Grain Direction
Metal sheets have an internal grain structure formed during manufacturing. Bending parallel to the grain increases the risk of cracking, while bending perpendicular to the grain improves flexibility and strength.
Common Methods of Bending in Sheet Metal
Various bending techniques are used depending on the material type, required shape, and production volume. Some of the most common methods include:
1. V-Bending
This is the most commonly used bending technique, where a V-shaped die and a punch are used to form a precise bend. It includes:
- Air Bending – The sheet is not fully pressed into the die, allowing for flexible angle adjustments.
- Bottoming – The metal is completely pressed into the die, resulting in accurate bends with minimal springback.
- Coining – Extreme force is applied to create an exact bend by imprinting the material with the punch and die.
2. U-Bending
Similar to V-bending, this method uses a U-shaped die to create curved bends for pipes, channels, and enclosures.
3. Roll Bending
In this technique, multiple rollers gradually bend the metal into cylindrical or curved shapes. It is used for making tubes, tanks, and curved structural components.
4. Edge Bending
This method involves clamping one edge of the sheet while force is applied to the opposite side, allowing for flange creation and edge reinforcements.
5. Rotary Bending
A rotary tool applies uniform pressure to bend the metal while minimizing surface damage. This method is suitable for cosmetic applications where aesthetics matter.
Applications of Bending in Sheet Metal
Bending in sheet metal is widely used across different industries to manufacture functional and structural components.
1. Automotive Industry
Bent sheet metal is essential for vehicle chassis, body panels, exhaust systems, and structural reinforcements. The process ensures lightweight yet durable components.
2. Aerospace Industry
Aircraft components such as wing supports, fuselage panels, and internal brackets require precise bending to meet strict safety and performance standards.
3. Construction and Infrastructure
Architectural elements such as roofing panels, staircases, and structural beams rely on sheet metal bending for strength and design flexibility.
4. Electronics and Appliances
Sheet metal bending is used to manufacture computer enclosures, air conditioning units, electrical panels, and household appliances.
5. Medical Equipment
Bent sheet metal is crucial for hospital beds, surgical instruments, and diagnostic machine enclosures, where accuracy and reliability are essential.
Advantages of Bending in Sheet Metal
There are several reasons why bending in sheet metal is a preferred fabrication method in modern manufacturing.
1. Material Efficiency
Since bending does not involve cutting or removing material, it reduces waste and optimizes material usage.
2. High Strength and Durability
Bending retains the structural integrity of the metal, making it stronger compared to welded or joined parts.
Read also: Blocked Drains Chelmsford and Drain Clearance Chelmsford
3. Cost-Effective Production
With automated CNC bending machines, manufacturers can achieve high-volume production with minimal labor costs.
4. Versatility in Design
Sheet metal bending allows for customized shapes and complex geometries, making it ideal for a wide range of applications.
5. Fast and Precise
Modern bending machines offer high-speed production with repeatable accuracy, improving efficiency.
Challenges in Bending in Sheet Metal
Despite its advantages, bending in sheet metal comes with some challenges that need to be addressed for optimal results.
1. Springback Issues
Springback can lead to inaccurate bends. Techniques like overbending or coining help counter this issue.
2. Material Cracking
Thin or brittle materials may develop cracks during bending. Choosing an appropriate bend radius and grain direction minimizes this risk.
3. Tool Wear and Maintenance
Repeated bending operations cause wear and tear on tools and dies, requiring regular maintenance and replacements.
4. Bending Limitations for Thick Sheets
While thin sheets are easy to bend, thicker sheets require specialized equipment and higher force, making the process more complex.
Modern Advancements in Sheet Metal Bending
With advancements in computer-controlled CNC bending machines, bending in sheet metal has become more precise and automated. Modern technologies include:
- Laser-guided bending for real-time accuracy.
- Programmable CNC press brakes for repeatability.
- Automated robotic bending to improve efficiency and reduce labor costs.
These innovations ensure high precision, reduced production time, and minimal material wastage, making bending more efficient than ever.
Conclusion
Bending in sheet metal is a fundamental process in metal fabrication that enables industries to create durable, lightweight, and cost-effective components. By understanding the different bending methods, key influencing factors, and modern advancements, manufacturers can improve efficiency and achieve high-quality results. As technology continues to evolve, the sheet metal bending process will become even more precise, automated, and versatile, meeting the growing demands of various industries.